Advertiser Disclosure: Eye of the Flyer, a division of Chatterbox Entertainment, Inc., is part of an affiliate sales network and receives compensation for sending traffic to partner sites, such as CreditCards.com. Some or all of the card offers that appear on the website are from advertisers. Compensation may impact how and where card products appear on the site. This site does not include all card companies or all available card offers. Opinions, reviews, analyses & recommendations are the author’s alone, and have not been reviewed, endorsed, or approved by any of these entities. Some of the links on this page are affiliate or referral links. We may receive a commission or referral bonus for purchases or successful applications made during shopping sessions or signups initiated from clicking those links.
The Boeing 737 has been a workhorse of the skies for over five decades — and a lot has changed since the very first 737. But what hasn’t changed has been its safety record. Besides the high profile cases, the aircraft is one of the most safe in the sky. Since 1959, the 737NG (-600/-700/-800/-900) family of aircraft averaged only 0.18 catastrophic (loss of life and/or airplane) accidents per 1 million departures. And, if we look at the 737MAX aircraft that number jumps to 1.48 catastrophic accidents per 1 million departures, a still incredibly low number, but it’s not just because it’s a well-built aircraft. The Boeing 737, and any aircraft for that matter, is rigorously inspected and checked daily to ensure airworthiness. Let’s explore the multitude of ways that a 737 is inspected to ensure safety.
Scheduled Inspections
Each commercial airline has a government-approved maintenance program to operate any aircraft that they fly. These inspections are routinely checked for accuracy and compliance by the airline’s own inspectors as well as government inspectors who are tasked with overseeing that airline.
Pre- & Post-Flight Walkarounds: Before every fight, the pilots do a walk-around of the aircraft. They are looking for large obvious issues to the aircraft, such as fluid leaking from the airplane, flat tires, and the overall exterior condition of the aircraft. The pilots are looking for anything immediately dangerous to the aircraft and are empowered to report and flag anything that looks out of place or unsafe. These happen before and after each flight, ensuring that anything that might have happened in the air or on the ground is caught. For the most part this catches almost all the threats to flight of the aircraft, however you can’t tell if failures are coming unless you rip the airplane apart.
A-Checks: Conducted every 500 flight hours, these focus on basic systems and components, like tires, brakes, and flight controls. These checks are preformed by qualified mechanics, these men and women have hundreds of hours of training before being allowed alone with the aircraft and become intimately familiar with the aircraft during their training. These 500-hour checks are like getting your oil changed at the mechanics. A more in-depth inspection is done under the hood, the tires are checked for replacement, all the fluids are checked to be within range, and everything is given a much deeper once over. These checks are also where heavier maintenance is done to the aircraft, if the plane has a reoccurring problem, it’s mostly diagnosed, fixed, or replaced at this stage.
B-Checks: These are more comprehensive checks, happening every 3,000-6,000 flight hours, they involve deeper inspections of engines, landing gear, and internal structures. This time, the aircraft will be pulled into the hangar for multiple days. These checks focus on large items with the aircraft such as the landing gear which is usually operated with the aircraft lifted on jacks. Break replacement, large component replacement, and larger maintenance issues are fixed during this stage. Due to the fact that maintenance personnel have a longer time with the aircraft, they get to address bigger ticket items. At this stage, engines are also checked with a borescope, looking for cracks inside the engine before it becomes a problem, and in some cases it could mean the entire engine is replaced before being cleared back into service.
C-Checks: The most intensive, occurring every 15,000-20,000 flight hours, it entails a near-complete disassembly of the aircraft for meticulous examination. Checks like these are also called “heavy check” and the aircraft is usually flown to a larger, more dedicated maintenance base or third party. Heavy Check rips the plane down to its core components to check everything from wiring to the airframe body for micro-cracks. This heavy maintenance usually occurs for a month or more at a time as everything on the aircraft is removed; panels, seats, lavs, and even the entire cockpit are removed. Because the aircraft has everything removed from the inside, this is also when airlines do things such as cabin remodels and aircraft painting. And lastly, just to be extra safe once the Heavy Check is complete, there is usually a check flight (only pilots onboard) to test all mechanical aspects of the airplane before it’s put back into service.
Government Oversight
Beyond the calendar, unforeseen events trigger additional checks. These checks are usually not apart from a routine maintenance procedure, but because something has changed and is mandated to be fixed or inspected. Airworthiness Directives (AD) are memos put out by the aviation governmental body, for the United States that’s the Federal Aviation Administration (FAA), to instruct operators to fix or replace a certain part of the aircraft outside established procedures. For example, after the waist door plug on an Alaska Airlines 737 MAX9 departed the aircraft while climbing out of Portland, the FAA issued an AD to all airline operators to inspect the door plugs. This type of AD has the authority to ground the aircraft until the directive has been complied with or give a deadline to which it has to be completed.
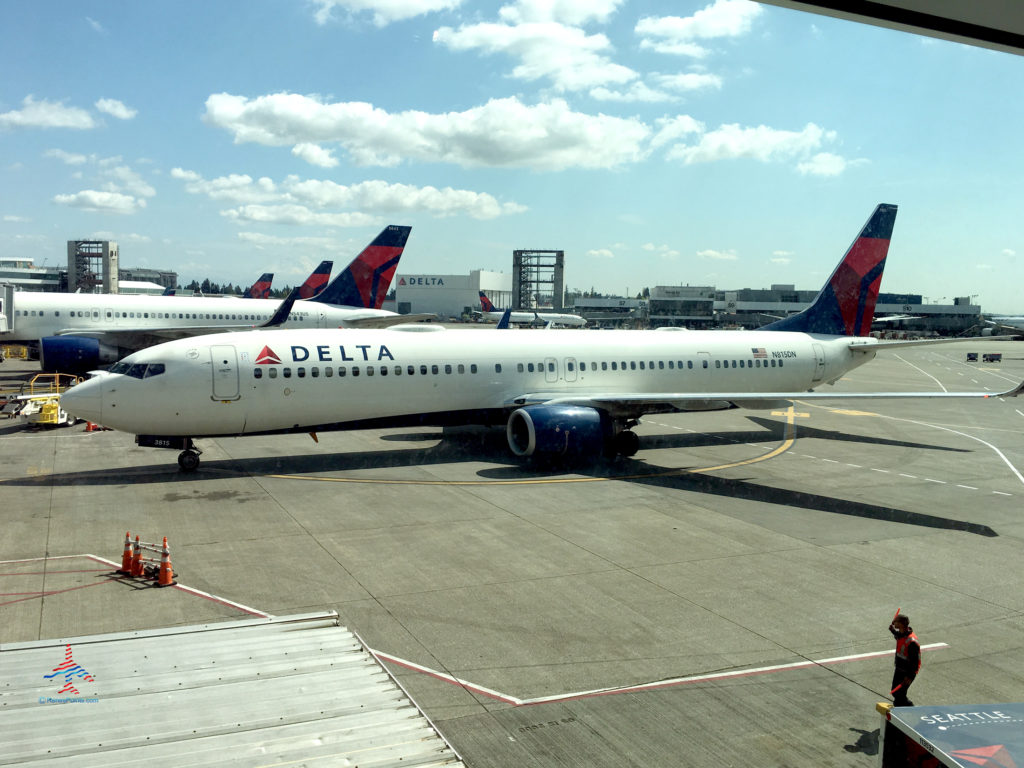
Non-Routine Maintenance
Lastly, when something breaks, you don’t just continue to fly around with something that’s broken. This non-routine maintenance is driven by a special book that all airlines possess called a Minimum Equipment List (MEL). The MEL book tells pilots, dispatchers, and maintenance what is allowed to be broken, how long it can be broken, if there are restrictions if it’s broken, and the minimum amount of working other components that must be operating for departure. For example, it’s easy to have one landing light broken while all the others function, but if they’re all broken then it’s pretty unsafe to fly at night. So if all landing lights are broken, you might only be allowed to do daytime operations, or if there is no MEL for all the landing lights not working, then maintenance will have to fix them. Whenever you do have a mechanical delay, it’s usually for this reason: there is no MEL for what is broken, and because it’s safety first, always no matter what, it has to be fixed.
Final Approach
The concern is very real any time there is an aircraft accident. However, the aviation industry learns from its mistakes, and almost every regulation or aircraft design change that there is has been the direct result of an incident that it never wants to repeat. As the National Transportation Safety Board (NTSB) and the FAA work together over the 737 MAX9 incidents (or any aircraft incident), their directives will result in that airplane becoming a safer aircraft. This may come in the form of regular checks to the seal of the aircraft or a new method to seal off the plug, the final verdict isn’t out yet. In the meantime, the FAA wouldn’t allow the aircraft to fly again if they didn’t think it was safe. I would feel very confident flying in a 737 MAX9 right by the waist door plug, however I’d much rather sit in first class for the comfort.
Advertiser Disclosure: Eye of the Flyer, a division of Chatterbox Entertainment, Inc., is part of an affiliate sales network and receives compensation for sending traffic to partner sites, such as CreditCards.com. Some or all of the card offers that appear on the website are from advertisers. Compensation may impact how and where card products appear on the site. This site does not include all card companies or all available card offers. Opinions, reviews, analyses & recommendations are the author’s alone, and have not been reviewed, endorsed, or approved by any of these entities. Some of the links on this page are affiliate or referral links. We may receive a commission or referral bonus for purchases or successful applications made during shopping sessions or signups initiated from clicking those links.
Responses are not provided or commissioned by the bank advertiser. Responses have not been reviewed, approved or otherwise endorsed by the bank advertiser. It is not the bank advertiser's responsibility to ensure all posts and/or questions are answered.
Odd to use a delta plane as the main image. Of the big US airline they are least exposed to Boeing and have no 737 Max.
@Justin – Keep in mind Delta has 100 of the 737 MAX jets on order with Boeing so just a matter of time (unless they convert order to another jet).
Keep in mind that the FAA recommended airlines with 737-900ER (i.e., Delta) inspect the door plugs.
Delta does have the 737-900 with the same door plug that blew out of Alaska’s Max 9. So they did a visual inspections. As a result of what they found, they then removed the door plugs of every 737-900 and reinstalled them correctly.